Optimizing Effectiveness and Quality With Cutting-Edge Metal Stamping Approaches
In the world of steel stamping, the quest of functional quality through the combination of ingenious techniques is extremely important. The junction of advanced steel stamping methodologies, automated systems, strict top quality controls, and lean production principles supplies an alluring peek into the future of production.
Advanced Steel Stamping Technologies
In the world of metal stamping, the combination of cutting-edge technologies has actually transformed the industry, enhancing precision and performance in making procedures - Metal Stamping. Advanced metal marking modern technologies have actually played a crucial duty in raising the abilities of manufacturers, permitting more intricate designs and greater manufacturing rates
One of the most substantial developments in metal marking modern technology is the execution of computer system numerical control (CNC) systems. CNC systems make it possible for specific control over the marking procedure, leading to exact and constant manufacturing of facility components. In addition, using servo presses has produced improvements in power effectiveness and decreased cycle times, further maximizing the production process.
Additionally, the integration of automation and robotics has structured metal marking procedures by increasing performance and lowering the threat of errors. Automated systems can execute jobs with speed and accuracy, bring about enhanced general effectiveness in the manufacturing line.
Automated Procedures for Efficiency
Use of automated processes in metal stamping operations has actually dramatically enhanced performance and productivity in producing facilities (Metal Stamping). Automated systems have transformed the steel stamping sector by simplifying procedures, reducing manual treatment, and minimizing the margin of error. These automated services encompass a variety of technologies, consisting of robotic arms, CNC devices, and computerized control systems, that work cohesively to carry out intricate stamping jobs with precision and speed
One main benefit of automated procedures in steel stamping is the constant top quality they deliver. By getting rid of human mistake and variants in manufacturing, automated systems ensure that each stamped part satisfies specific specifications with minimal problems. Automation makes it possible for continuous operation, significantly minimizing downtime for device adjustments and upkeep, therefore optimizing total performance.
In addition, automated procedures improve security in metal stamping operations by minimizing the need for hand-operated handling of hefty products and sharp tools. This not just safeguards employees yet likewise contributes to a more structured and effective workflow. Finally, the integration of automated procedures in metal stamping procedures is critical for attaining optimum effectiveness, quality, and safety and security criteria in contemporary manufacturing environments.
Quality Control Actions in Stamping
Given the focus on constant quality and performance accomplished through automated procedures in steel stamping procedures, applying robust quality assurance actions comes to be essential to promote criteria and guarantee precision in stamped components. Quality control in steel stamping entails a multi-faceted technique to ensure the integrity and precision of the end products. Assessment checkpoints at various stages of the marking process are vital to determine any deviations from specs early on. Using innovative technologies such as electronic vision systems and automated dimension tools can enhance the speed and precision of quality examinations. Statistical procedure control approaches assist in monitoring and managing the stamping process to detect any type of variants that can impact high quality. Additionally, training programs for staff on high quality requirements and treatments are essential to ensure that everyone involved comprehends and adheres to the established quality assurance procedures. By incorporating these actions into steel stamping operations, makers can continually generate top quality stamped parts that meet the strict requirements of contemporary sectors.
Enhancing Accuracy With Development
To achieve unrivaled accuracy in steel stamping procedures, pioneering developments are continuously being created and incorporated into the production workflow. Advanced technologies such as laser reducing systems and computer numerical control (CNC) equipments have actually transformed the way steel parts are stamped with utmost precision. By using laser cutting modern technology, makers can achieve complex and complex designs with micron-level accuracy, making sure that each stamped component satisfies the most strict high quality criteria.
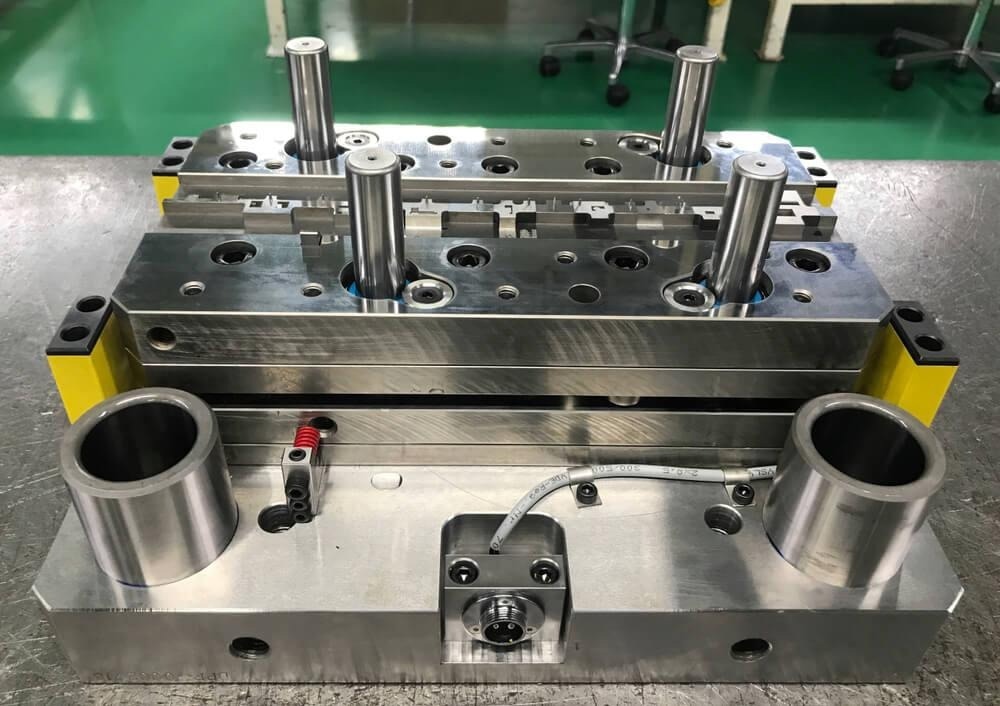
Furthermore, making use of simulation software enables suppliers to analyze and maximize stamping processes before actual manufacturing, determining prospective areas for improvement and fine-tuning parameters to attain optimum accuracy. By welcoming these cutting-edge innovations, producers can enhance precision, rise effectiveness, and deliver top notch stamped products that meet one of the most rigorous demands of modern sectors.
Carrying Out Lean Production Practices
Incorporating lean production methods into steel stamping procedures can cause streamlined production procedures and enhanced overall effectiveness. By concentrating on removing waste, enhancing resources, and continually improving processes, steel stamping firms can improve productivity and top quality while lowering expenses. One essential aspect of applying lean manufacturing in steel stamping is the focus on producing a smooth and effective operations. This includes arranging workstations, systematizing procedures, and reducing unnecessary movements to take sites full advantage of efficiency.
Additionally, lean production practices encourage a culture of constant renovation within the company. By empowering workers to determine and resolve ineffectiveness, firms can make step-by-step changes that result in considerable efficiency gains gradually. Applying devices such as five, Kanban systems, and worth stream Read Full Report mapping can aid streamline operations, decrease preparations, and improve total top quality in metal stamping processes.
Final Thought
Finally, the utilization of advanced steel marking technologies, automated procedures, quality assurance measures, development for precision enhancement, and execution of lean production techniques are important for taking full advantage of performance and top quality in steel marking procedures. These methods make sure that items are created with consistency, cost-effectiveness, and precision. By integrating these cutting-edge techniques, producers can stay affordable in the sector and fulfill the needs of clients successfully.
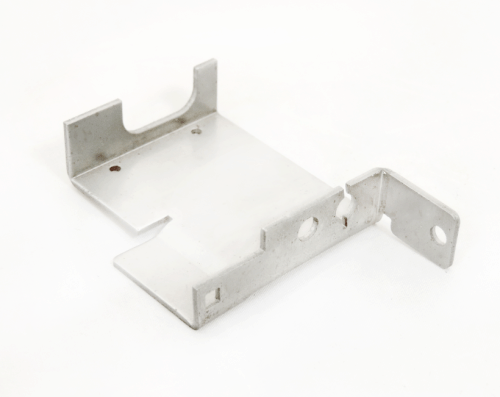
Provided the focus on regular top quality and efficiency achieved with automated processes in metal stamping operations, carrying out durable top quality control actions comes to be crucial to make sure and maintain requirements accuracy in stamped components. Carrying out devices such as Five, Kanban systems, and value stream mapping can go to the website help enhance procedures, minimize lead times, and improve general high quality in metal stamping procedures.
In verdict, the application of advanced metal marking modern technologies, automated procedures, top quality control actions, technology for accuracy enhancement, and application of lean manufacturing techniques are crucial for making best use of performance and high quality in metal stamping operations.